- GD&T
GENERAL DIMENSIONING- International Paper Size Standards
- Technical Drawing Styles
- ISO And ANSI Projections
- ANSI Technical Drawing Views
- Technical Drawing Dimesioning Types
- ANSI and ISO Geometric Tolerancing Symbols
- Geometric Tolerancing Reading
- Taylor Principle Rule#1
- Form Tolerances
- Profile Tolerances
- Orientation Tolerances
- Location Tolerances
- Runout Tolerances
- TOLERANCES
ANSI AND ISO- Tolerancing and Engineering Standards
- Hole and Shaft Basis Limits And Fits
- ISO International System For Limits And Fits
- International Tolerance Grade (IT)
- Fundamental Deviations For Hole and Shaft Basis
- ISO Tolerance Band IT01-IT16
- Calculation Of International Tolerance
- Calculation of Upper and Lower Deviation For Shaft
- Calculation of Upper and Lower Deviation For Holes
- ISO Shaft Tolerances (3mm-400mm)
- ISO Shaft Tolerances (400mm-3150mm)
- ISO Hole Tolerances (3mm-400mm)
- ISO Hole Tolerances (400mm-3150mm)
- ANSI Standard Limits and Fits
- METAL CUTTING TECHNOLOGIES
- Terms and Definitions of the Cutting Tools
- Cutting Tool Materials
- Selection of Carbide to machine the work-part
- Identification System For Indexable Inserts
- Work-Part Materials
- Machinability and the specific cutting force
- Machinability of the Certain Material Evaluations
- Cutting Forces and Chip Formations
ISO N; NON-FERROUS MATERIAL
Nonferrous Metals and Alloys
Nonferrous metals and alloys cover a wide range of materials from the more common metals such as
aluminum, copper, and magnesium, to high-strength high-temperature alloys such as tungsten, tantalum and molybdenum.
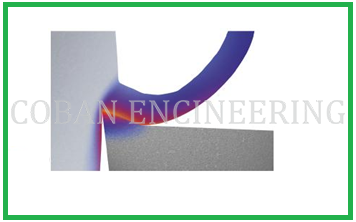
Although more expensive than ferrous metals, nonferrous metals and alloys have important applications because of their numerous properties, such as corrosion resistance, high thermal and electrical conductivity, low density, and ease of fabrication. This group contains non-ferrous, soft metals with hardnesses under 130 HB, except for high strength bronzes (>225HB). Aluminum (Al) alloys comprising less than 12-13% silicon (Si) represent the largest part. MMC: Metal Matrix Composite: Al + SiC (20-30%). Magnesium based alloys. Copper, electrolytic copper with 99.95% Cu. Bronze: Copper with Tin (Sn) (10-14%) and/or aluminum (3-10%). Brass: Copper (60-85%) with Zinc (Zn) (40-15%)
Aluminum: Aluminum is a very lightweight work-piece material. Aluminum has great strength for its weight. Aluminum has been an excellent material for farming structures in commercial and military. Aluminum corrosive resistance has made it very popular work-piece material for variety of industry. Most grades of Aluminum are easily machined. Aluminum strength and hardness can be increased by alloying with silicon, iron, nickel, manganese, chromium etc. when work-piece material machined on Turning or drilling, Chips are continuous type, they are limiting safety factor because they tend to bunch up over the cutting tools. Machinability of aluminum; Long-chipping material, Relatively easy chip control, if alloyed Pure Al is sticky and requires sharp cutting edges and high vc Specific cutting force: 50,750-101,500 lbs/inch² (350–700 N/mm² ). Cutting forces, and thus the power required to machine them, are low. The material can be machined with fine-grained, uncoated carbide grades when the Si-content is below 7-8%, and with PCD- tipped grades for Aluminum with higher Si-content. Over eutectic Al with higher Si-content > 12% is very abrasive.
Copper: it is very popular material that is widely used for its superior electrical conductivity, corrosion resistance etc. When alloyed properly with other elements, copper alloy can exhibit a vast array of strength level and unique machinability and mechanical properties. Copper alloys are in widespread commercial use. Including Brasses, Bronzes, Copper- Nickels, lead copper, Copper-Nickel-Zinc alloys etc. The Copper machinability and its alloys vary widely. High Copper alloys and Pure Copper are very tough, abrasive and prone to tearing. These types of work-piece materials should be machined with positive rake angle cutting tools geometries. For Bronze and its alloys due to their ductility and toughness positive rake angle cutting tool should be used. Brass and Its alloys because of their similarity of chip formation to cast iron, Negative axial and positive rake angle cutting tools geometries should be used for better machinability.
ISO S; HEAT RESISTANT SUPER ALLOYS (HRSA)
Superalloys, also known as heat-resistant superalloys or high-temperature alloys, are materials that can be machined at temperatures exceeding 1000˚ F (540˚ C). No other alloy system has a better combination of high temperature corrosion resistance, oxidation resistance, and creep resistance. Because of these characteristics, superalloys are widely used in aircraft engine components and in industrial gas turbine components for power generation. They are also utilized in petrochemical, oil, and biomedical applications, specifically for their excellent corrosion resistance. Classifications of Superalloys; High-temperature alloys are broadly classified into three groups: nickel-base, cobalt-base, and iron-nickel-base alloys, and Titanium Based alloys
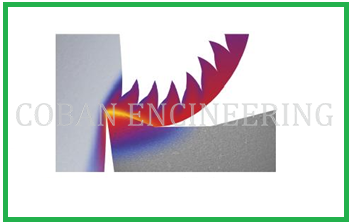
Nickel-Base Superalloys
Among the high-temperature alloys, nickel-base alloys are the most widely used. As a result,
they are often found in aerospace engine and power generation turbine components, as well as in petrochemical,
food processing, nuclear reactor, and pollution control equipment. Nickel-base alloys can be strengthened
by two methods: through solid solution strengthening or by being hardened through intermetallic compound
precipitation in fcc matrix. Alloys such as INCONEL 625 and Hastelloy X are solid solution strengthened.
These solid solution hardened alloys may get additional strengthening from carbide precipitation.
Alloys such as INCONEL 718, however, are precipitation strengthened. A third class of nickel-base
superalloys, typified by MA-754, is strengthened by dispersion of inert particles such as yttria (Y2O3),
and in some cases with γ´ (gamma prime) precipitation (MA-6000E). Nickel-base alloys are available
in both cast and wrought forms. Highly alloyed compositions, such as Rene 95, Udimet 720, and IN100,
are produced by powder metallurgy followed by forging. For the above wrought alloys and for cast alloys
(Rene 80 and Mar-M- 247), the strengthening agent is γ’ precipitate. For INCONEL 718, γ˝
(gamma double prime) is the primary strengthening agent. Alloys that contain niobium, titanium, and aluminum,
such as INCONEL 725, are strengthened by both γ´ and γ˝ precipitates. Nikel is often used
to improve corrosion, heat resistance, and strength of many materials as alloying element. When Nickel
is alloyed with copper which is called as Monels. When Nickel is alloyed with Chromium which is called
as Inconels and Hastelloys. When Nickel is alloyed with Chromium and Cobalt Which is called as Waspalloys.
Nickel provides a vast array of alloys, which exhibit a wide range of physical properties. Also there
are some other important alloys belong to these group Astroloy, Rene, Incoloys, Haynes, Udimet alloys.
The Nickel based alloys machinability are generally quite hard.Material Characteristics of Nickel-Base
Superalloys; High forces at the cutting edge, High heat concentration in cutting area. High cutting
speed may cause insert failure by plastic deformation, relatively poor tool life, Small depths of
cut are difficult, Rapid workhardening, and usually abrasive rather than hard.
Troubleshooting when cutting Nikel based superalloys;
Problem of Depth-of-cut notch: Solution for it; Increase toolholder lead angle. Use tougher grades in -MS, -MP, and -RP
geometries or ceramic grade in cutting tools. Use a 0,63mm/.025" or greater depth of cut. Depth of cut should be
greater than the workhardened layer resulting from the previous cut (>0,12mm/.005"). Program a ramp to vary depth of cut.
Feed greater than 0,12mm/.005 IPR. Use strongest insert shape possible. When possible, use round inserts in carbide grade.
Decrease depth to 1/7th of insert diameter for round.
Problem of Built-up edge: Solution for it; Increase speed. Use better grades of cutting tools. Use positive rake, sharp PVD coated grades. Use flood coolant.
Problem of Chipping: Solution for it; Use MG-MS geometry in place of MG-FS or GP geometries. For interrupted cutting, maintain speed and decrease feed. Use a tougher grade of the cutting tools.
Problem of Torn Work-piece surface finish: Solution for it; Increase speed and reduce feed rate. Use a GG, FS or GT-HP geometry.
Problem of Work-piece glazing: Solution for it; Increase depth of cut. Increase feed rate and decrease speed. Reduce insert nose radius size.
Cobalt-Base Superalloys
Cobalt-base superalloys possess superior corrosion resistance at temperatures above 2000˚ F (1093˚ C)
and find application in hotter sections of gas turbines and combustor parts. Available in cast or wrought iron form,
cobalt-base superalloys are characterized by a solid solution strengthened (by iron, chromium, and tungsten),
by an austenitic (face centered cubic or fcc) matrix, in which a small quantity of carbides (of titanium, tantalum, hafnium, and niobium)
is precipitated. Thus, they rely on carbides, rather than γ´ precipitates, for strengthening, and they exhibit better
weldability and thermal fatigue resistance than nickel-base alloys. Cast alloys, such as Stellite 31, are used in
the hot sections (blades and vanes) of gas turbines. Wrought alloys, such as Haynes 25, are produced as sheet,
and are often used in combustor parts. Material Characteristics of Cobalt-Base: Superalloys; High forces at
the cutting edge, High heat concentration in cutting area. High cutting speed may cause insert failure
by plastic deformation. Cast material more difficult to machine than wrought. Relatively poor tool life.
Small depths of cut are difficult. Rapid workhardening, and usually abrasive rather than hard.
Troubleshooting when cutting Cobalt-Base Superalloys;
Problem of Depth-of-cut notch: Solution for it; Increase toolholder lead angle. Use a tougher carbide
grade or ceramic grades. 3. Use a 0,63mm/.025" or greater depth of cut. Program a ramp to vary depth of cut.
Feed greater than 0,12mm/.005 IPR. Use strongest insert shape possible. Depth-of-cut should be greater than
the work-hardened, layer resulting from the previous cut (greater than 0,12mm/.005").
Problem of Built-up edge: Solution for it; Increase speed. Use positive rake, sharp PVD coated grades, Use ceramic grades.
Problem of Chipping: Solution for it; Use MG-MS geometry in place of GG-FS or GP. For interrupted cutting, maintain speed and decrease feed.
Problem of Torn Workpiece surface finish: Solution for it; Increase speed. Reduce feed rate. Use a GG-FS, GT-HP, or GT-LF geometry.
Problem of Workpiece glazing: Solution for it; Increase depth of cut. Increase feed rate and decrease speed. Reduce insert nose radius size.
Copyright ©2010-2023 Coban Engineering.All Rights Reserved.